Risk Assessment (DHAs & EPDs)
Before preventative and protection strategies may be identified, a risk assessment is necessary to identify where combustible dust hazards exist within your facility. Fike performs risk assessments around the world to meet NFPA 652 requirements of a Dust Hazard Analysis (DHA) and ATEX 1999/92/EC regulations of an Explosion Protection Document (EPD).
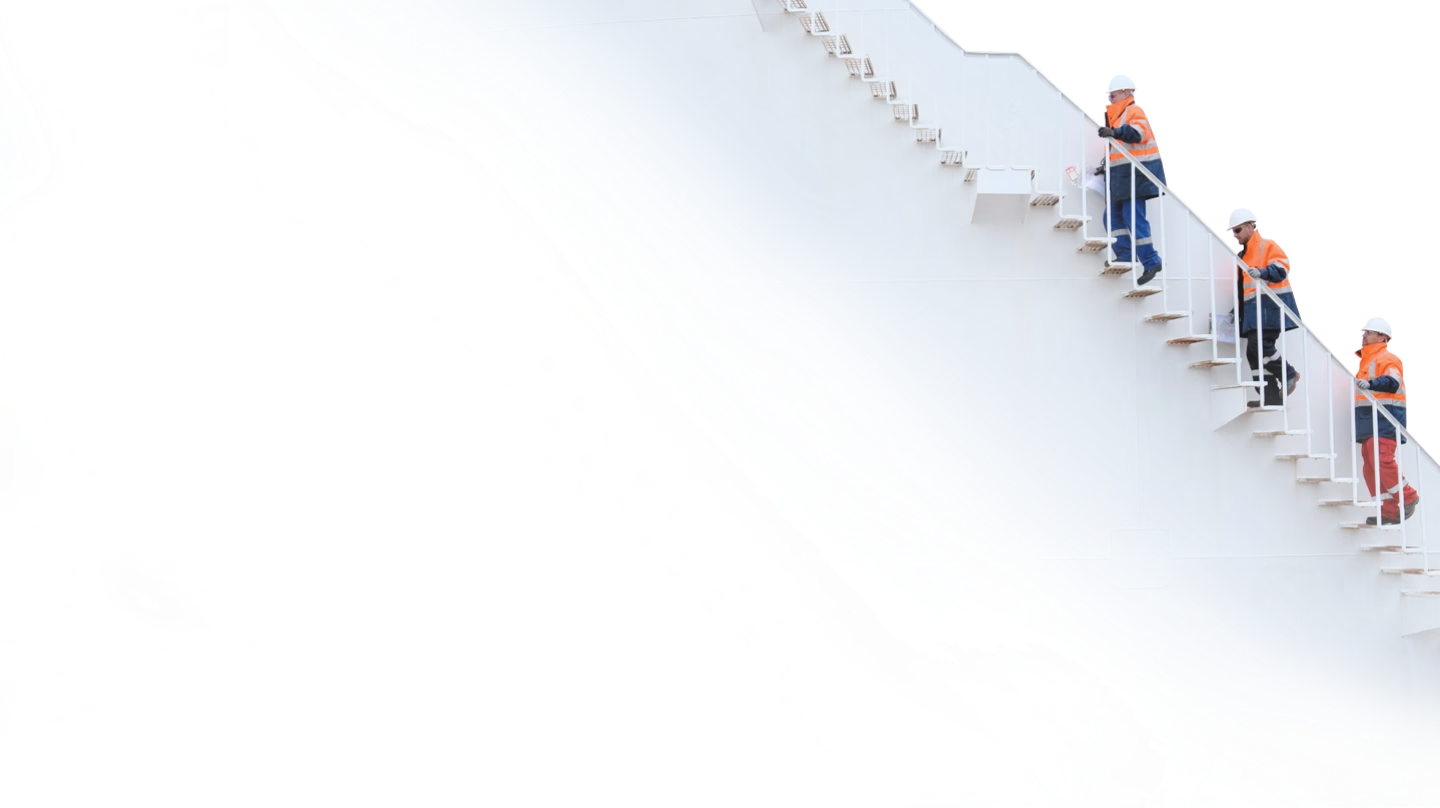
What is Included in a Fike Risk Assessment?
Identify Hazardous Zones
Uses existing process flow diagrams, anecdotal evidence from your experts and a facility walkthrough to understand which areas of your process should be analyzed further and which areas are considered low risk and may largely be ignored.
Analyze Materials & Flammable Atmospheres
Of the identified hazardous zones, further analysis will be perform on where dust is being introduced, conveyed or emitted, where dust clouds develop and where a potentially flammable or explosive atmosphere may occur. Reviews the documented explosibility of the dust handled in the process and performs dust testing if necessary.
Review Ignition Sources & Safeguards
Locates and evaluates potential ignition sources (sparks, static, overheated surfaces and more) which could produce an explosion. Evaluates your safety systems and housekeeping processes to ensure they are compliant and effective. Further opportunities to reduce the risk of combustion will be documented in the final DHA/EPD report.
Create an Action Plan
Prioritizes the areas of your process which should be addressed immediately based on the likelihood of an explosion from occurring and its potential severity. Furthermore, relatively simple or cost-effective areas to improve safety will also be recommended as high priority.
How Can a Risk Assessment be Used to Improve Safety at Your Facility?
Your Fike consultant will use the results from dust testing and identify opportunities within your process to lower the risk of combustion from ever occurring by reducing or removing the following ignition sources:
- Open Flames or Heat
-
welding, cutting, or smoldering items
- Electrical Sparks
-
when a high-voltage device fails or a cable ruptures
- Hot Surfaces
-
combustion equipment, heated processes, motors and lights
- Electrostatic Discharge
-
when equipment or containers are not grounded properly
- Frictional Heat or Sparks
-
overheated bearings or other malfunctioning equipment
- Smoldering Material
-
which slowly combusts internally as long as oxygen is present
- Unisolated Explosions
-
secondary explosions which consume additional fuel and grow in intensity
- Rogue Objects
-
such as a bolt entering the system and creating friction or sparks
Other explosion prevention efforts may include:
- Improving housekeeping in areas with dust accumulation
- Performing regular maintenance on equipment, such as lubricating bearings, to keep surface temperatures below those found in a Minimum Ignition Temperature (MIT) dust test
- Installing spark detectors or reducing risk of static discharge to align with data found in a Minimum Ignition Energy (MIE) dust test
- Identify opportunities to mitigate through inerting the process environment with data found in the Limiting Oxygen Concentration (LOC) dust test
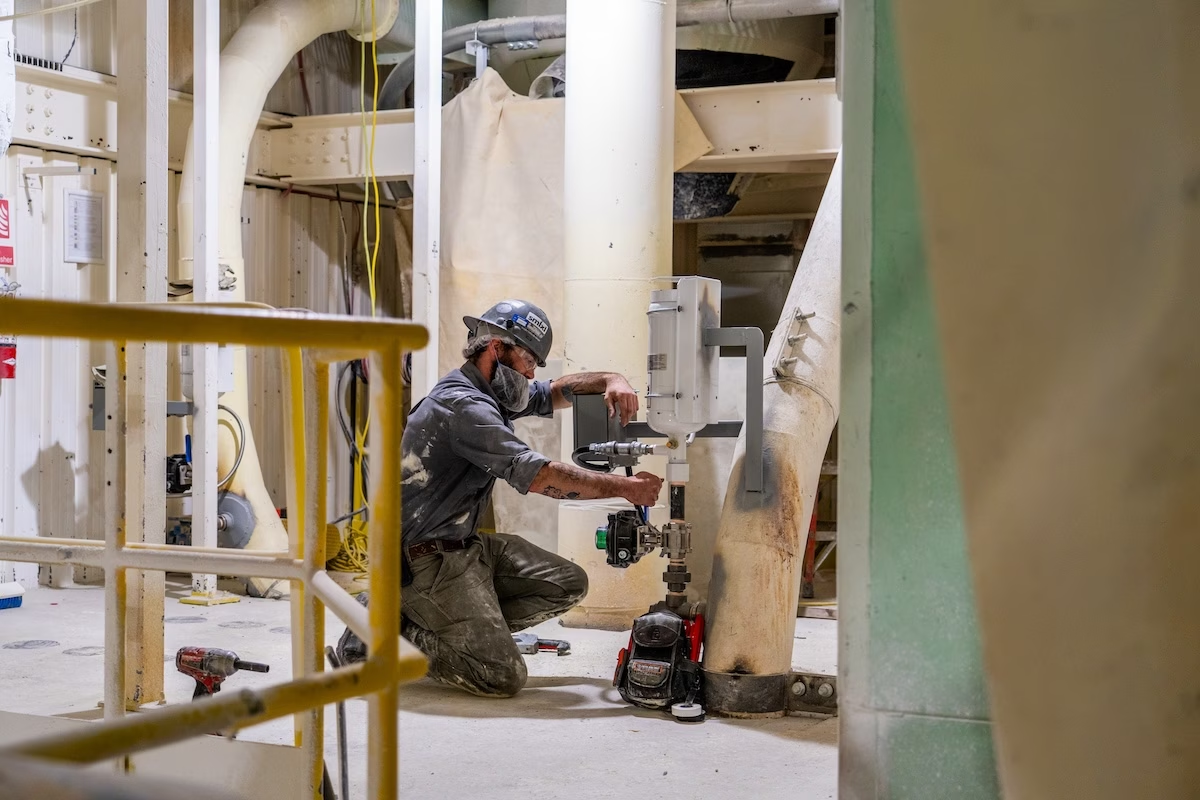
Why Choose Fike to Perform Your Risk Assessment?
We know you have many options when choosing a partner to complete your DHA or EPD. By working with Fike to complete your risk assessment, you can expect the following:
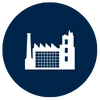
Unmatched experience completing risk assessments for nearly all industries and their unique processes, equipment and combustible materials.
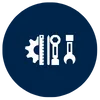
Nearly any recommended explosion protection system or service identified in the risk assessment can be designed, manufactured, installed, commissioned and maintained by Fike.
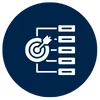
The most reliable and cost-effective solution to improve safety will always be recommended, whether it does or doesn’t include Fike products and services.
Meet The Fike Consultancy Experts
Our consultants have combined experiences exceeding 75 years of field combustion hazard consulting. They offer objective insight into what hazards exist in your facility, how to address each hazard in both priority and efficiency.
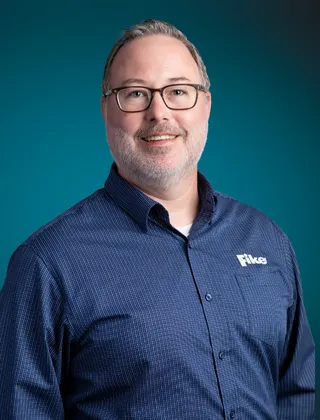
Brian Edwards, PE
- Licensed civil and environmental engineer.
- 20 years experience in safety and environmental consulting.
- Member of NFPA Industrial Fire Protection Section, and past experience sitting on NFPA 61 and 664.
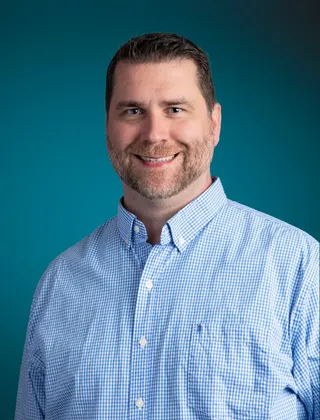
Jeff Davis, PE
- Licensed professional engineer.
- 15 years of consulting with a focus on combustible dust, gases and liquids, and OSHA's PSM and EPA's RMP standards.
- Member of NFPA; previously a principal member on NFPA 61, 91, 654, 655, and 664.

Bruce McLelland, CET
- NICET IV-certified in special hazards technologies.
- 47 years of testing, researching, designing product and managing in industrial safety.
- Current principal committee member on NFPA 652, NFPA 654, NFPA 655, NFPA 91, NFPA 664 and NFPA 61.
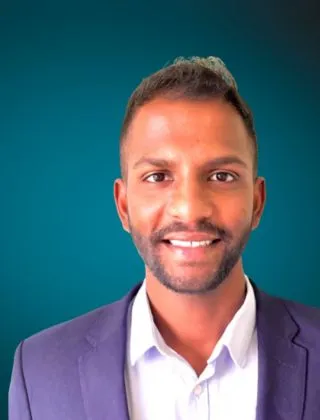
Dilip Arulappan, MSc
- MSc process safety and loss prevention engineering
- More than 10 years of engineering and process safety consulting experience
- Member of IChemE Process Safety and an Exida certified Functional Safety Professional
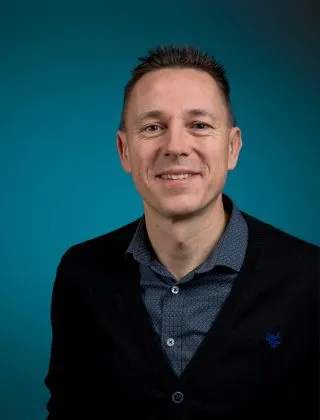
Jim Vingerhoets, MSc
- Civil Engineer
- More than 15 years of experience in explosion safety, risk assessments, consequence modelling, protection technology and design, engineering and innovation
- Delegate in European Standardization Committee CEN/TC305
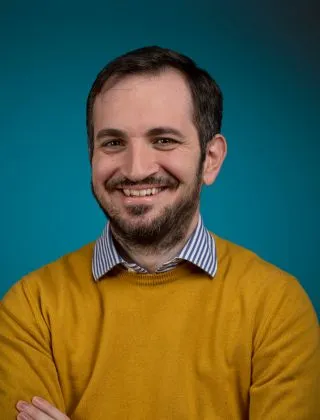
Dimitrios Kakogiannis, PhD
- Mechanical and Aeronautical Engineer
- 16 years of experience in R&D of emerging technologies for military and industrial applications in the domain of explosion protection
- Currently active working member of European Standardization Committee CEN TC 305 WG3